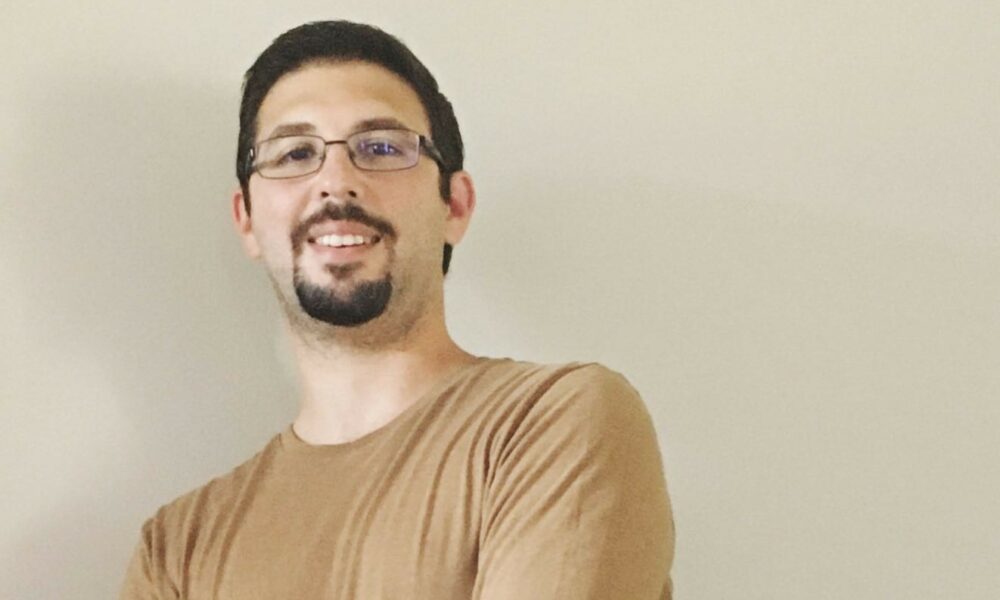
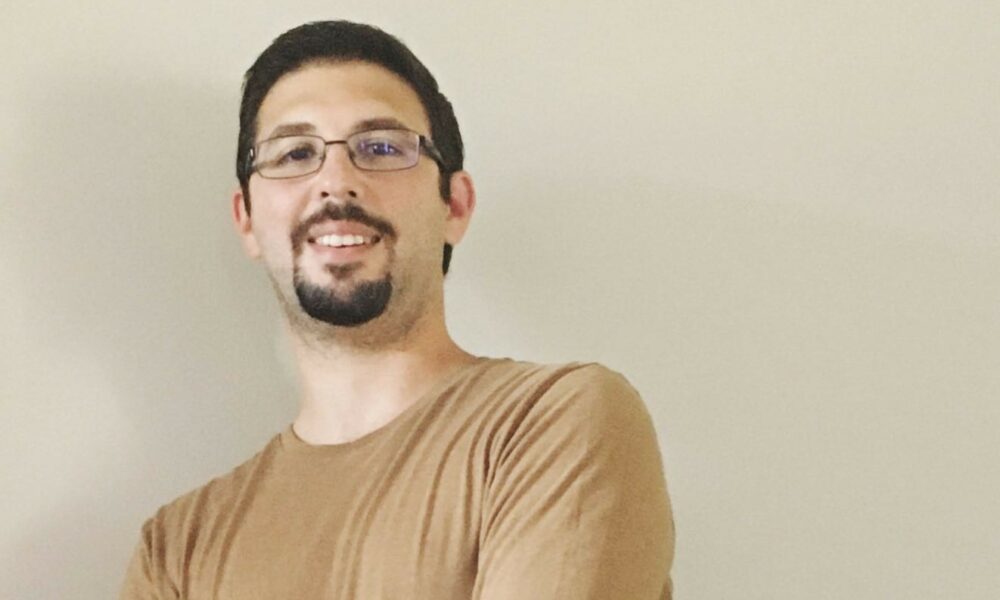
Today we’d like to introduce you to Anthony DiMambro.
Hi Anthony, it’s an honor to have you on the platform. Thanks for taking the time to share your story with us – to start, maybe you can share some of your backstories with our readers.
When I began studying computer science in school some years ago, a local violin shop based in southeast Michigan was looking for a tech person. As you can imagine, they were still running software from the ’80s, and this was an excellent opportunity to work for a small business while focusing on school. As I continued in my position at the shop, my scope of roles increased tremendously. At some point, one of the owners developed some serious tendinitis and wasn’t able to keep up with the bow work. After outsourcing the work without any success, it was at the suggestion of violin maker Jonathon Price that the shop train me to do rehairs and bow maintenance. Showing aptitude with technical information as well as sharp hand-eye coordination, this is where I began my journey into the field of bow work.
While I enjoyed the work, the learning process was rather brutal. Not everyone is a natural-born teacher, and thorough education was hard to come by. Being a little sheltered from other bow makers and without much direction, I wasn’t too sure where to turn, but I was hungry. I spent countless hours reading on the associated trades to bow work as there weren’t any good texts on the subject easily attainable. I read through a number of books on jewelry making, clock/watchmaking, woodworking, and machining.
My employer was a student of the famed American bow maker Bill Salchow. Mr. Salchow was a former instructor for summer workshops at the University of New Hampshire (UNH) and long considered the father of American bow making. Looking to expand my abilities, my employer was able to send me to a UNH workshop on advanced bow repair with George Rubino. Eventually, I ended up working full-time at the local shop as I enjoyed the work at the bench and working with musicians. And now, armed with a more concrete base for bow work, I spent all my time behind the bench practicing. Accruing thousands of rehairs, tip plates, windings, etc., under my belt.
Weeks turned into months, and months to years, spending over a third of my life behind the workbench at the shop. I learned much about proper tool use, the history of makers, and came into contact with a lot of really nice bows and musicians. I’m so thankful for all my experiences there, the good, the bad, and the ugly, as even the hard lessons can cause one to grow tremendously.
All throughout the history of instrument and bow makers, there is a definite tradition of working as an apprentice for an established workshop for approximately ten years. Then venturing off on your own to establish your own workshop. I more than paid my dues, diligently working, giving back to the business to help the business grow and flourish.
I spent nearly 10 years focusing on bow maintenance and repair before ever getting into bow making. I finally felt that I had a good handle on anything you could do with a bow and that the only way I’d get a deeper understanding was to make a bow.
I tried my hand at a making few bows alone, the first 3 were fairly rough, but I managed to make the stick, frog, and button on them. It was a huge learning experience both in bow making and in tool making as well. Not knowing where to turn, I just figured I hunker down and make a bunch of bows.
In 2017, I made the leap to start my own firm, AD Bows, LLC. I had my own ideas of what customer service should look like. Skill-wise, I was hitting a plateau; I was hungry to grow but was being held back by being forced to adhere to antiquated techniques and ideas of repair and restoration. It was even frowned upon to involve yourself with the greater community of makers and shops. I finally had enough and wanted to share my passion with people on my own terms.
During this transition, I started working with award-winning bowmaker Rodney Mohr at Learning Trade Secrets, located in Ashland, Ohio. I used to have to beg, borrow, and steal to get any tidbits of useful information; Rodney is an excellent instructor and shares information without holding back. I feel like my bow-making had jumped up several notches just in working with him. If you are interested in bow-making, I can’t stress enough to find an excellent mentor as early as possible to get you off to a great start. The knowledge I have gained from Rodney has proven invaluable, and not only count him as one of my teachers but as a mentor as well.
I am also passionate about passing on information and teaching the next generation. In 2020, I completed a book about the unique and specialized tools that bow makers use. This is done in an attempt to break down one of the barriers of entry into bow-making. Many specialized tools are not commercially available or are extremely cost-prohibitive due to small batch productions. The ability to make one’s own tools is a necessary skill for any bow maker or restorer. This manual should prove to be a useful resource and great place to start for those bow makers new to tool making.
I now have a partnership with violinmaker Jonathan Price, who suggested I get into bow work from the very beginning of this story. Our business, Michigan Strings, LLC, is located in Southfield, Michigan. Not only do we service many clients in Michigan, but we have many clients in the Toledo Symphony, and with Oberlin Conservatory of Music, and Bowling Green State University. Additional to local clients, we have clients that span across the United States and Canada that own our instruments and bows and seek us out for expert repair and maintenance.
We all face challenges, but looking back, would you describe it as a relatively smooth road?
I wouldn’t say so. It was difficult having a discouraging employer and learning new skills when much of the information out there is considered trade secrets that many aren’t willing to share. Owning your own business requires not just knowledge in your field, but concepts of marketing, bookkeeping, accounting, web design, etc. So while not a smooth road, it’s always exciting to be challenged and to grow and learn new things.
Can you tell our readers more about what you do and what you think sets you apart from others?
I enjoy making bows for musicians. I love when a musician approaches me to commission a bow. I listen and watch how the musician plays; I have them play several bows, I listen to their violin and observe their playing technique, I talk with them about their desired feel and sound from a bow. All the while, I’m developing a picture of what the finished bow will look like. The height of the head, the curve, and thicknesses of the stick, the artistic stylings to name just a few. Every time I make a bow for a player, they are always so pleased with it, and for me, that is so rewarding. It’s like making a custom suit or dress, but a bow that is tailored specifically to fit someone’s playing style. I also enjoy making baroque bows, bows designed for early music. These bows have so much room for artistic expression, and I get really geeky about studying and researching these types of bows when making a modern reproduction.
We’d be interested to hear your thoughts on luck and what role, if any, you feel it’s played for you.
I don’t believe in luck, just hard work. You and the people you surround yourself with are solely responsible for making things happen or not happen. Even when bad things happen, do you have systems in place to deal with such things, do you have a support group of good people to help you out. Kind of like prepare for the worst, and hope for the best attitude. When things come easy or just happen, it’s usually a result of all the hard work you put in coming to fruition.
Contact Info:
- Website: www.adbowsllc.com
- Instagram: https://www.instagram.com/adbowsllc/
- Facebook: https://www.facebook.com/ADBowsllc
- Youtube: https://www.youtube.com/channel/UCqn6a9o2tF9KltfqxnQsFZw